用于制造诊断和监测设备的医用级硅橡胶
通过高性能诊断和可穿戴设备预防疾病
护理点检测(POCT)是一项重要的诊断趋势,可快速准确地确定疾病。我们相信预防总是比治疗好。我们的医用级硅胶是一种化学惰性解决方案,可用于少量和大量生产可靠的 POCT 设备。
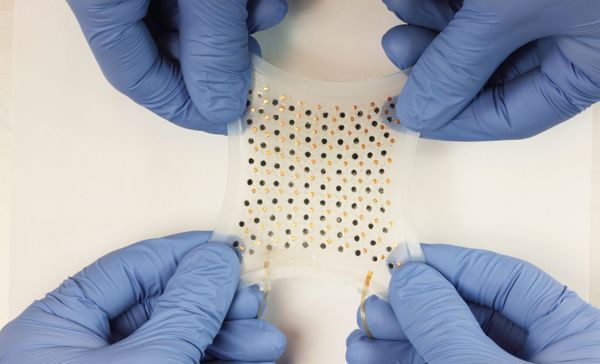
我们相信预防胜过治疗
用于制造体外诊断设备的医用级硅橡胶
用于制造体外诊断设备的医用级硅橡胶
护理点体外诊断(IVD)检测(POCT)是诊断领域的一个新兴趋势,因为它们包括患者的一次性和家庭健康选项。POCT 设备易于使用,无需前往医疗机构,可在几分钟内提供测试结果,因此非常方便。除此之外,微流体卡式瓶是 POCT 装置的核心。这些芯片凝结在几厘米处,可进行抽样、样品制备和各种参数的平行分析。有机硅有利于微米级制造和阀门、微型泵和其他组件的集成。利用 Silbione™ 有机硅材料将为体外诊断点测试装置的制造商提供各种益处,包括生物相容性和应用特定的解决方案,以限制蛋白质和药物的吸收。
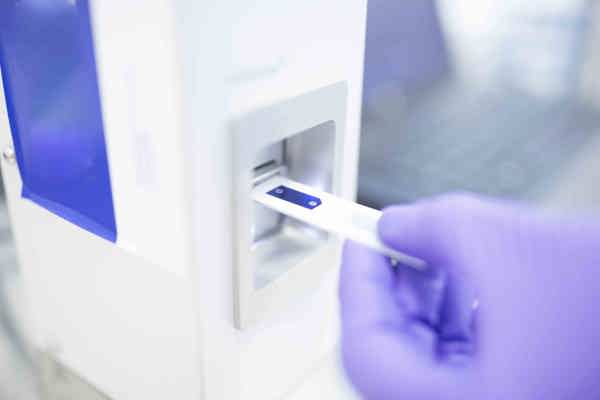
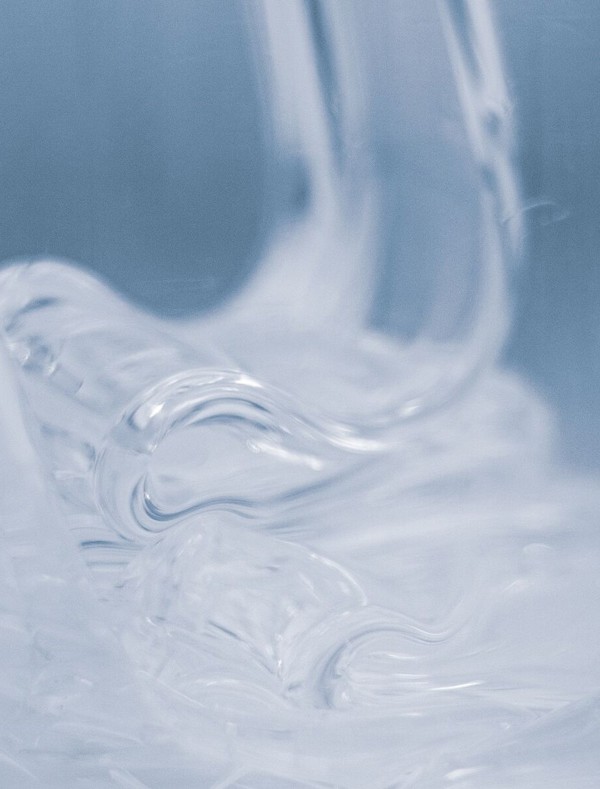
用于可穿戴解决方案的硅胶
硅胶可穿戴解决方案,与客户的高科技要求保持同步
活动跟踪器和连续葡萄糖监测器或血压监测器等可穿戴设备可让用户跟踪其健康和保健数据。必要时,直接访问这些数据有助于采取适当的护理措施。由于这些装置可以长时间直接佩戴在皮肤上,所用材料必须具有舒适性并且过敏性低。 对于皮肤贴片,Silbione™ 柔性皮肤粘合剂是传统丙烯酸基粘合剂的完美替代品,因为柔性有机硅皮肤粘合剂可以无痛地移除并能多次重新定位。
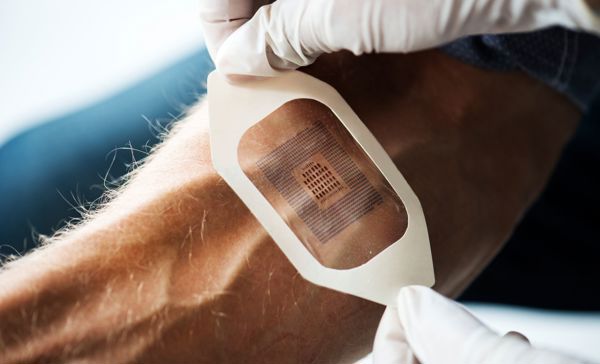
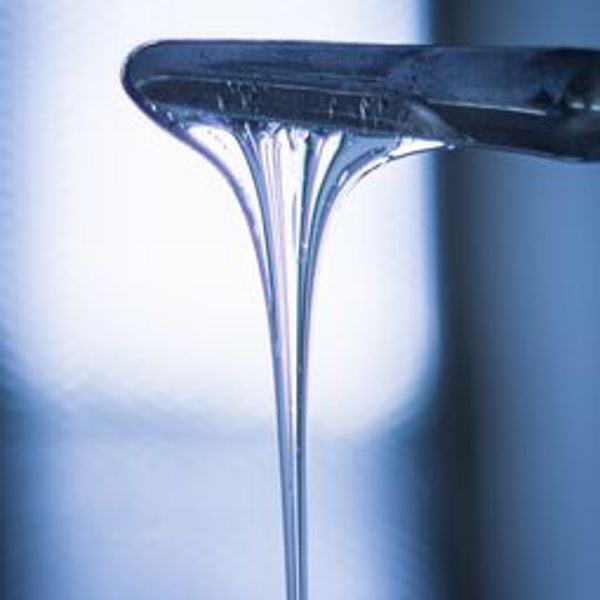
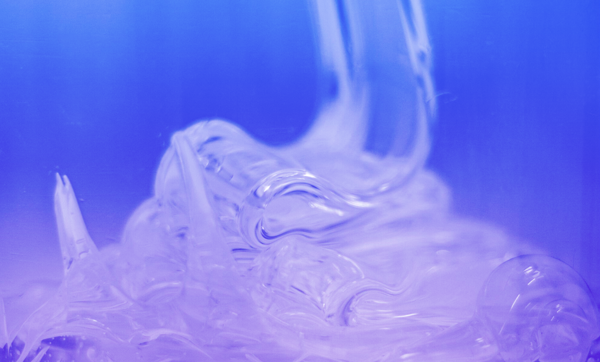
埃肯医用级有机硅,全方位赋能医疗器械创新制造
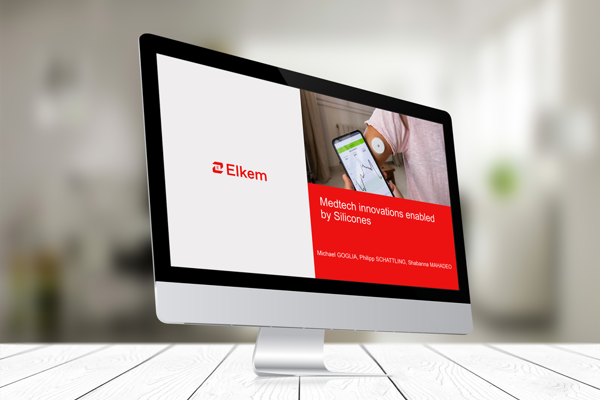
联系我们
与全球领先的材料制造商携手,将您的企业提升到一个新的水平。